Injection Molding Design Guidelines: A Complete Manufacturing Guide for 2025
Master the art of injection molding design with expert guidelines for optimal manufacturing results. Learn essential principles, best practices, and cost-saving strategies from industry veterans.
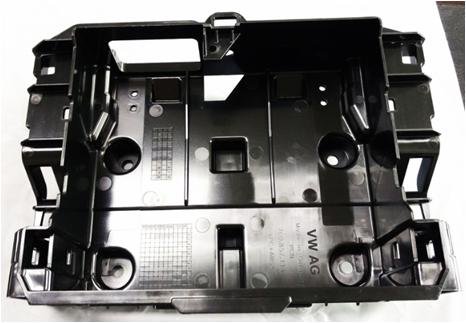
Injection Molding Design Guidelines: A Complete Manufacturing Guide for 2024
In today's precision-driven manufacturing landscape, mastering injection molding design guidelines is crucial for product development success. As an industry veteran with over two decades of experience working with leading injection molding manufacturers in China, I've witnessed how proper design considerations can dramatically impact product quality and manufacturing efficiency. This comprehensive guide will walk you through essential principles that ensure manufacturability while optimizing costs.
Understanding the Fundamentals of Injection Molding Design
Before diving into specific guidelines, it's essential to understand that successful injection molding begins with proper design considerations. Working with an experienced plastic mold design specialist can significantly impact your project's success rate and final product quality. The key to excellence lies in understanding the intricate relationship between part design, material selection, and processing parameters.
Critical Design Parameters for Injection Molded Parts
When designing parts for injection molding, several key parameters require careful consideration:
- Wall thickness uniformity plays a crucial role in preventing warpage and ensuring proper material flow throughout the mold cavity. Consistent wall thickness helps maintain uniform cooling rates and minimizes internal stresses.
- Draft angles must be incorporated to facilitate easy part ejection, typically ranging from 1° to 3° depending on the surface texture and depth. Proper draft angles reduce tool wear and improve part quality.
- Corner transitions should be designed with appropriate radii to prevent stress concentration and ensure proper material flow. Sharp corners can lead to molding defects and structural weaknesses.
- Gate location planning affects the final part quality and influences the occurrence of weld lines and sink marks. Strategic gate placement optimizes material flow and part aesthetics.
Material Selection Impact on Design Decisions
Material Type | Shrinkage Rate | Recommended Wall Thickness | Common Applications | Processing Temperature |
---|---|---|---|---|
ABS | 0.4-0.7% | 1.2-3.5mm | Consumer Electronics | 220-260°C |
Polypropylene | 1.0-2.5% | 0.8-3.8mm | Packaging | 200-280°C |
Polycarbonate | 0.5-0.7% | 1.0-3.8mm | Medical Devices | 280-320°C |
Nylon | 0.8-2.0% | 1.0-3.0mm | Automotive Parts | 240-280°C |
Wall Thickness Optimization Strategies
Proper wall thickness design is fundamental for successful injection molding. Consider these essential guidelines:
- Maintain uniform wall thickness throughout the part to prevent warpage and sink marks. Variations in thickness can lead to differential cooling rates and part defects.
- Design walls within the recommended thickness range for your chosen material, typically between 1.0 to 3.0mm for most applications. This ensures optimal material flow and cooling characteristics.
- Implement gradual transitions when thickness changes are necessary, using a maximum ratio of 3:1 to prevent stress concentration and flow issues.
Advanced Design Considerations for Complex Parts
Complex injection molded parts require additional design considerations:
- Multi-cavity mold designs need careful balancing of runner systems and flow paths to ensure consistent part quality across all cavities. This includes considering gate locations and sizing for optimal filling patterns.
- Incorporating design features that facilitate automated part removal and handling can significantly reduce cycle times and labor costs. This might include ejector pin locations and pickup points for robotic handling.
- Understanding the relationship between material selection and processing parameters helps optimize both design and production efficiency. Different materials require specific processing conditions and design accommodations.
Design for Manufacturing (DFM) Best Practices
Implementing DFM principles early in the design phase can significantly impact production success:
- Conduct thorough mold flow analysis to identify potential issues before tool construction begins. This proactive approach saves both time and resources in the long run.
- Consider the impact of material selection on tool design and processing parameters. Different materials require specific design considerations for optimal performance.
- Design parts with appropriate draft angles to reduce cycle time and improve productivity. This includes considering both internal and external surfaces.
- Minimize undercuts to reduce tool complexity and maintenance requirements. When unavoidable, design them for efficient manufacturing.
Cost Optimization Through Strategic Design
Implementing cost-saving measures through design requires careful consideration of several factors:
- Material selection and optimization can significantly impact overall production costs. Choose materials that balance performance requirements with cost-effectiveness.
- Tool design complexity directly affects both initial tooling costs and ongoing maintenance expenses. Simplify designs where possible without compromising functionality.
- Cycle time optimization through proper design can lead to substantial cost savings in high-volume production. Consider cooling time requirements in your design decisions.
Quality Control and Testing Considerations
Ensure your design facilitates proper quality control:
- Include measurement reference points for critical dimensions. These should be easily accessible and clearly defined in the design documentation.
- Design appropriate test features for functional requirements. This might include specific geometry for strength testing or assembly verification.
- Consider incorporating traceability features like date codes or part numbers. These should be designed for clear visibility and durability.
- Plan for in-process quality checks that can be performed efficiently during production.
Future Trends and Innovations
Stay ahead of the curve by considering emerging trends in injection molding design:
- Integration of Industry 4.0 principles into mold design and production monitoring enables real-time quality control and process optimization.
- Advanced simulation tools provide more accurate prediction of part behavior and process parameters, reducing development time and costs.
- Sustainable design practices are becoming increasingly important, including material selection and end-of-life considerations.
- Smart mold technologies incorporating sensors and monitoring systems improve production efficiency and part quality.
Final Design Review Checklist
Before finalizing your design, ensure you've addressed these critical aspects:
- Verify all wall thicknesses are within recommended ranges for the selected material.
- Confirm appropriate draft angles on all vertical surfaces.
- Review gate locations and runner system design for optimal material flow.
- Ensure all critical dimensions are properly toleranced and measurable.
- Validate that the design meets all assembly and functional requirements.
By following these comprehensive guidelines and working closely with experienced injection molding partners, you can achieve optimal results in your plastic part production. Remember that successful injection molding design is an iterative process that requires attention to detail and continuous improvement.
What's Your Reaction?






